Brentwood Medical, a leader in thermoformed medical device packaging, maintains a 30,000 square-foot cleanroom in Reading, PA. The company’s commitment to excellence and meticulous attention to detail has propelled it to the forefront of cleanroom packaging production. By undergoing yearly recertification and adhering to strict employee cleanliness standards, Brentwood has solidified its position as a superior plastic manufacturing company, surpassing the capabilities of most other rigid packaging producers that only maintain ISO Class 8 or 9 cleanrooms.
The Birth of Brentwood’s First Cleanroom
In 1980, Brentwood took a significant step towards establishing its reputation of packaging excellence by creating its first white room at its original headquarters in Reading, Pennsylvania. Cleanrooms are specialized environments that maintain exceptional air quality by minimizing the presence of contaminants, ensuring optimal manufacturing conditions. By adhering to the rigorous standards outlined by the International Organization for Standardization (ISO), Brentwood distinguished itself as an industry leader in delivering products of exceptional quality. Over the years, the company’s Reading, Pennsylvania, cleanroom evolved, undergoing upgrades and an expansion. Today, it spans over 30,000 square feet and is certified to ISO Class 7 standards, surpassing industry benchmarks.
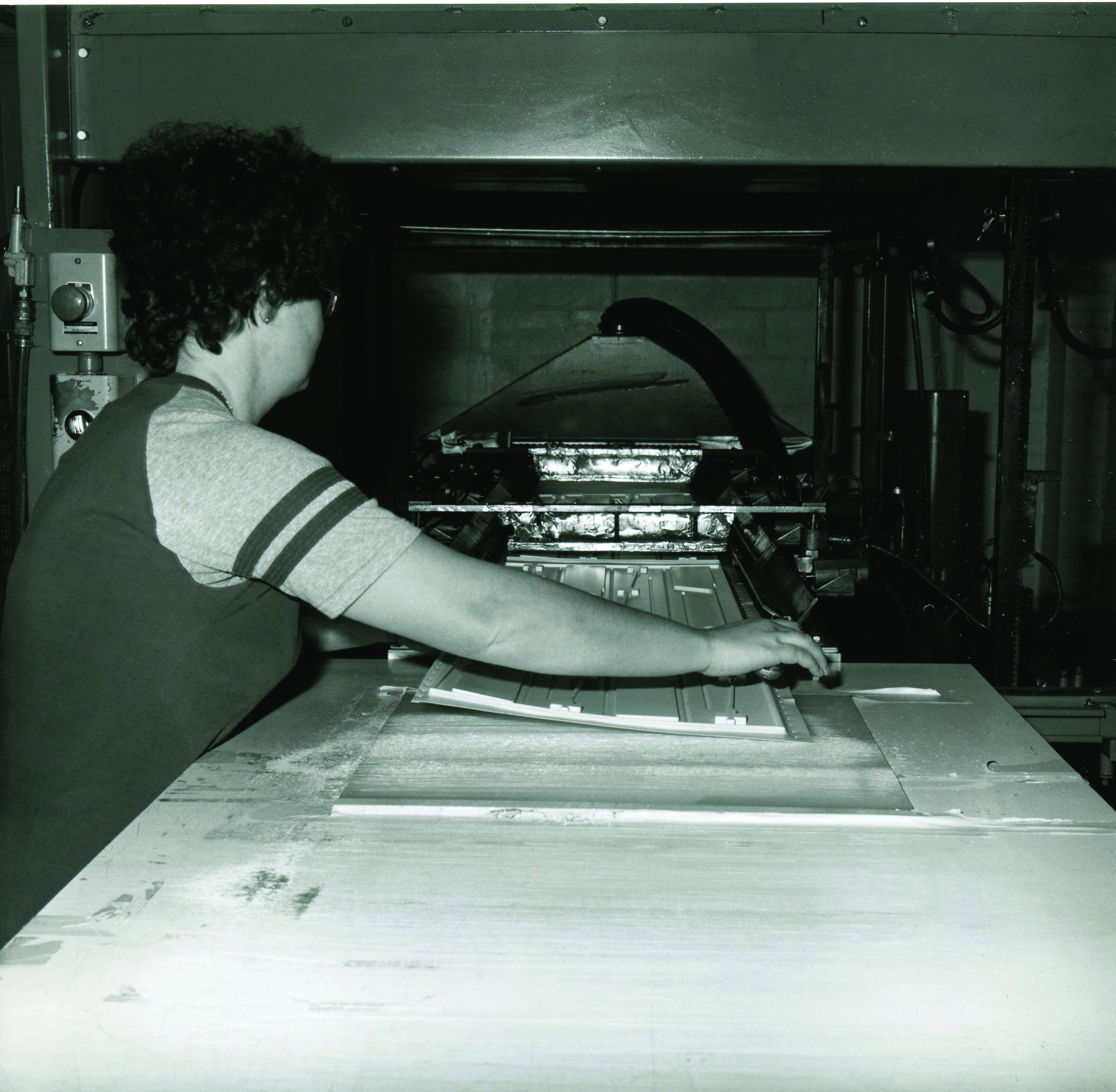
Ensuring Continuous Excellence
Brentwood’s commitment to delivering products of the highest quality is evident in the annual recertification processes its cleanroom undergoes. Each year, the cleanroom facility undergoes thorough evaluations to verify compliance with ISO Class 7 cleanroom standards. These evaluations involve rigorous inspections, testing procedures, and comprehensive analysis to ensure the cleanroom consistently meets the prescribed air quality and cleanliness levels. By maintaining these stringent requirements, Brentwood guarantees that customers receive products that meet and exceed their quality specifications.
0 Comments